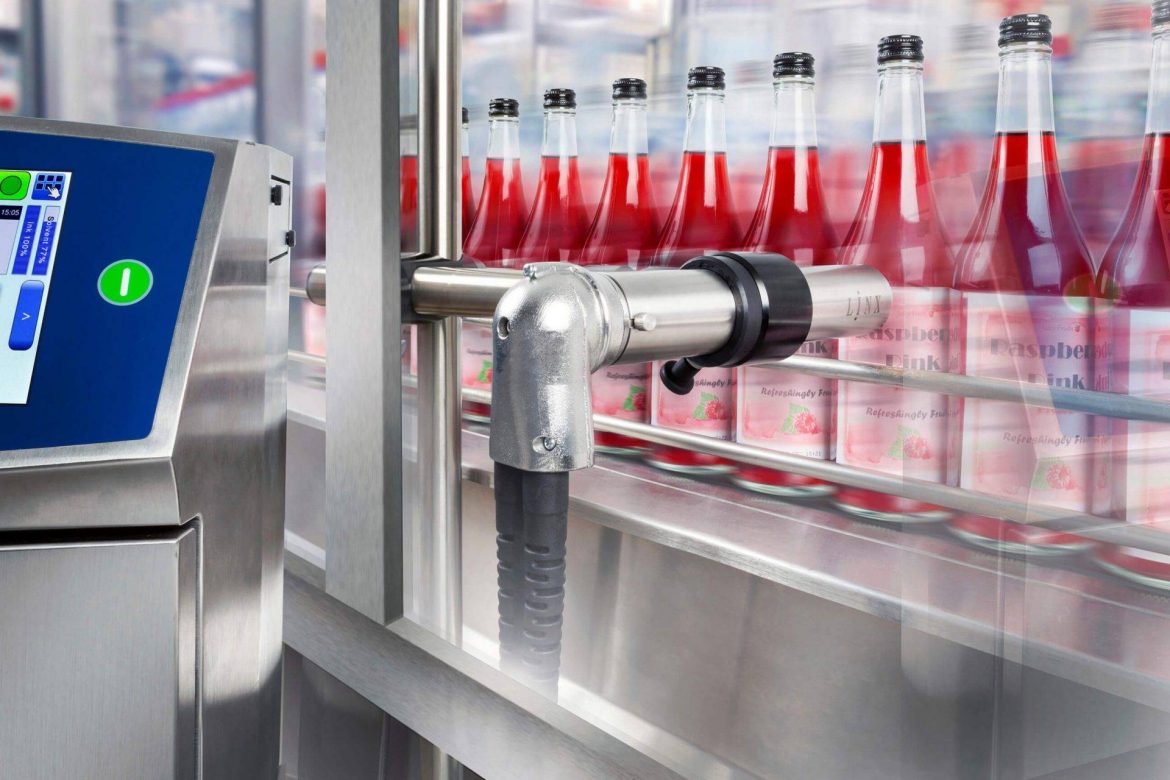
Solution for high speed and efficient production: inkjet printer for bottles
The Beverage industry often needs to have high speed production. This is to cut costs and to improve the efficiency of production. Improve speed and reduce costs in your beverage line with inkjet printers for bottles—ideal for cold, wet, and high-volume environments. Boosting production means improving every stage in production, including using a high-speed bottle printer to handle your coding and labelling needs. This article will present to you why a particular inkjet printer for bottles is needed for your beverages production process.
The challenges of printing onto a bottle’s surface
When considering the challenges of printing on bottles, it’s important to evaluate not just the printer itself but also the type of ink being used. Advanced ink formulations designed for specific materials and environments can significantly improve adhesion, durability, and legibility. Investing in the right ink ensures that your product labeling remains intact throughout the supply chain.
You know how printing onto a paper is a total 180 turn compared to printing onto a bottle’s surface, especially curved bottles commonly used in the beverage industry. It has different material, for one, different surface shape, and it has different texture. In fact, bottles itself have many different shapes and textures.
That hasn’t counted the environment in which you must print your label onto the product. Ink bleeds in a wet environment, so what ink is the best for that?
1. The environment
There are many manufacturing environments, you should be aware of the condition of yours.
Enclosures are the first things you need to pay attention to for printers. Printers that aren’t properly secured or left open during operation will affect the printer performance. Dirt, dust, grease, and oil may clog up your printer, reducing its performance.
Inkjet printer is secured, in this case, allowing neither dust or dirt to get into the machine with a fastened enclosure. Sure, you still have to do maintenance every once in 12 months or so, but it is more of a check instead of a full maintenance. This makes inkjet printers an excellent bottle coding machine for continuous operations with minimal interruption.
Damp, Wet, and Cold Environment
Additionally, inkjet printers can be equipped with special nozzles and ink systems to maintain consistent performance even in extreme conditions. For instance, solvent-based inks designed for cold and wet environments provide excellent adhesion and fast drying, reducing smudging and improving production line efficiency.
In the beverage industry, it is common for production rooms to be colder to sustain the quality of the drinks. This usually causes moistures to form on the bottle, and make the environment damper and wetter.
A lot of printers may not be able to print in this particular environment, but that is not the case for inkjet printers. Inkjet printer for bottles is set up such that it can resist water, shooting through any moisture on the surface, directly to the bottle.
The machine itself is protected from the environment, making sure it won’t go down because of technical issues.
2. The material of the bottle
Another critical consideration is the recyclability of the packaging. As sustainability becomes a priority in the beverage industry, many manufacturers are shifting toward eco-friendly materials. Modern inkjet printers support this initiative by using non-toxic, environmentally friendly inks that adhere well to both recycled and recyclable plastics.
The material of a bottle can make a world difference in what type of ink and what type of printer you can use. In general, there are two types of material used to make a bottle, glass bottle and plastic bottle.
Glass bottle
Glass has existed far longer than anyone would expect. Looking back, every wine bottle in the cellar is made of glass, and it’s not for no reason.
Glass has such an elegant and classy look to it that people just feel compelled to admire. Add to it the right beverage; people will flock to buy your products.
Printing on it, however, is a tough question to answer. You can print 3D on it using heat, or with modern technology, you can use an inkjet printer for bottles.
Inkjet printer can spray its ink to the glass with a precise and elegant look too. Be it for dates, labels, or batch numbers, inkjet printers can do them.
Plastic bottle
Plastic bottles have been very popular for some decades, cutting production costs far more than using glass for packaging. Printing a plastic bottle using a thermal printer is not a choice like a glass bottle, having a high risk of melting or dent.
Advanced inkjet printers, like those designed for PET bottles, provide superior adhesion and fast-drying inks that resist environmental factors like moisture and temperature changes, ensuring codes remain clear and legible throughout the product’s lifecycle. These features are crucial for maintaining traceability in the beverage industry.
Inkjet printers came with the right solution to print onto plastic bottles, especially PET bottles that are commonly used due to their cost-effectiveness and recyclability. It has the right speed, the right ability to survive the environment of the factory, and it can shoot to plastic.
3. The shape of the bottle
Bottles have different shapes, but most have curves that make printing harder. This also made direct printing out of the question. Non-contact printing has saved this printing for a long time, though.
Non-contact printers vary, from thermal, inkjet, to laser.
Among these, inkjet printers are considered the most practical bottle labelling solution due to their balance of affordability, speed, and adaptability to bottle shapes. Thermal printer results may be more pronounced, but it costs more. Lasers cost even more. To cut the cost, inkjet is probably the right choice. However, if you are in the pharmaceutical industry and in need to have more sophisticated labels on your products, laser printers are your best bet.
Beyond the shape of the bottle, it’s essential to consider the production speed required. High-speed inkjet printers are specifically designed to handle large volumes without compromising on print quality. These printers are equipped with advanced software that ensures precision even at maximum speeds, making them ideal for fast-paced manufacturing lines.
Why printing on a bottle and why inkjet printer is your solution
In addition to providing unmatched accuracy and durability, inkjet printers also offer significant flexibility. With the ability to print various fonts, graphics, and barcodes, these printers can cater to diverse labeling needs, from branding to regulatory compliance. This adaptability ensures that your product stands out on the shelf while meeting industry requirements.
Printing directly onto a bottle can affect the design of your products. It can also build trust as printing directly on glass or plastics means it cannot be copied as easily.
Hard to copy products will mean that your product’s counterfeit is more likely to exist. With less possibility of this, the efficiency of your distribution is. In the event of recall, if it happened at all, it will be easy for you to trace your products as printing labels directly on a bottle is likely to get erased.
Last but not least, with cutting cost and the speed, inkjet printer for bottles can boost your production times better than other kinds of printers. It is precise with low downtime, making the loss of production during maintenance can be minimized.
Conclusion
Inkjet bottle printers have revolutionized the manufacturing industry by providing high-speed, reliable, and versatile printing solutions. These printers are ideal for various bottle types, ensuring high-quality and durable prints that enhance product presentation and compliance with industry standards. By investing in an inkjet bottle printer, manufacturers can significantly boost their production efficiency and maintain consistent quality across all products.
See Also CIJ Printer Recommendation for Reducing Your Total Cost of Ownership
Comments (0)
Leave a reply
You must be logged in to post a comment.