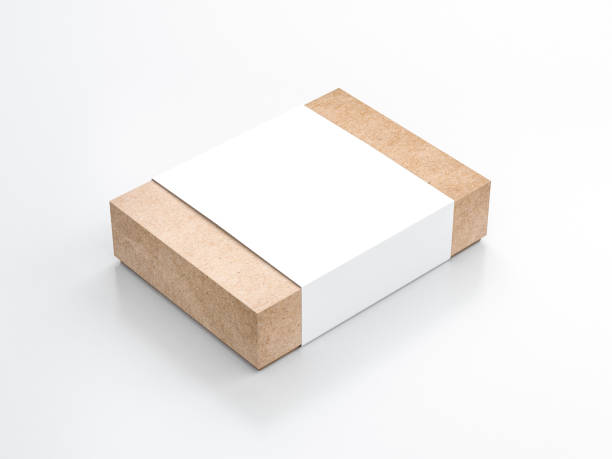
Despite its advantages, printing on sleeves presents unique obstacles that need careful preparation and appropriate solutions. Challenges such as ink adhesion, misalignment, and production speed can impact print quality and regulatory compliance.
In this article, we’ll explore the key challenges of code printing on sleeve packaging and the best solutions to achieve high-quality, durable markings.
Sleeve packaging (or packaging sleeve) has been very popular owing to its flexibility and low cost. Also known as sleeve wraps or wrap-around packaging, it is seen as a creative and practical method of protecting and marking items.
Despite its advantages, printing on sleeves presents unique obstacles that need careful preparation and appropriate solutions. Let’s explore them all here!
Understanding Sleeve Material Challenges
Essentially, sleeve packaging is a printed strip of material—usually paper or plastic—wrapped around a product. Sleeves, unlike boxes, do not have a top or bottom, making them a more economical and efficient choice.
They are widely utilized in various sectors, including electronics, food and beverage, and cosmetics since they provide an appealing method to display critical information such as branding, product features, and regulatory codes.
Its flexibility in customization is among its most important advantages. Companies may build a unique design that reflects their personality by selecting from various materials, sizes, and finishes. For instance, adding die cuts, lacquer, or embossing enhances the appearance, and unique dimensions ensure that the items fit snugly.
However, there are disadvantages to this ease of use and adaptability, especially in terms of programming. Because of the material properties and how sleeves fit around things, it may be challenging to print critical information like batch numbers or expiration dates onto sleeves. These are a few of the challenges:
Adjusting to Surface Variations
Sleeve packaging often wraps around products with irregular shapes, which creates surface variations that make printing tricky.
For example, a bottle’s curve or the sleeve’s uneven texture can distort printed codes and make them hard to read. Even small shifts in position during production (known as “print drift”) can lead to misaligned or incomplete codes.
Also, manufacturers need help with securely positioned sleeves on the product. Minor fluctuations in angle or position might degrade print quality as packaging passes through manufacturing lines.
Historically, UV sensors maintained accuracy by detecting a fixed reference point on the sleeve. However, with the push toward more sustainable practices, UV-cured inks are becoming less common, so manufacturers need to find alternative solutions.
One solution is using smart vision systems combined with AI-driven alignment software. These systems analyze the sleeve’s position in real time and adjust the printing process automatically.
Read About: Understanding Print Resolution and Code Readability for Food Products
Choosing the Right Printing Technology
Now you know that you need alternatives to printing on sleeves, another challenge is choosing the right printing technology, as it can significantly affect the quality and reliability of the codes.
To guarantee that the finished product satisfies both practical and aesthetic requirements, the printing process on sleeve packaging often consists of many processes. First, the sleeve is designed, frequently using a decline based on the product’s measurements.
Here, the divine acts as a blueprint, defining the shape and layout of the sleeve. Once the design is finalized, it’s time to decide on materials and additional finishing touches like embossing or varnishing.
The actual printing procedure is usually carried out on a large-scale commercial printer. After printing, the sleeves may undergo additional processes like scoring (to enhance foldability) or die-cutting (to create unique shapes). Finally, the printed sleeves are folded into their final form or left flat for easier shipping and storage.
While this procedure is uncomplicated, it is far from simple in terms of coding. As alternatives, Continuous Inkjet Printers (CIJ) and Thermal Inkjet Printers (TIJ) are two standard marking and labelling methods for sleeve packaging. Here is the difference:
- CIJ Printers: These are ideal for high-speed production lines and can print on various surfaces, including curved or uneven ones. CIJ printers use fast-drying inks that are suitable for products requiring immediate handling.
- TIJ Printers: Known for their precision, TIJ printers are excellent for producing high-resolution codes like QR codes or small text. They’re perfect for applications where clarity is critical.
So, which one is the best? Well, both technologies offer unique benefits. CIJ printers are best for speed and durability, while TIJ printers excel in detailed printing. Thus, the choice depends on your production needs.
When to Choose CIJ vs. TIJ for Sleeve Packaging:
- Choose CIJ if: You require high-speed printing, durable ink adhesion, and resistance to harsh environments.
- Choose TIJ if: You need sharp, high-resolution printing for barcodes, QR codes, and expiration dates.
Additionally, integrating these printers with Industry 4.0 systems like Manufacturing Execution Systems (MES) and Enterprise Resource Planning (ERP) can further enhance efficiency. This ensures real-time monitoring, minimizes downtime, and maintains compliance with industry standards.
Managing Environmental and Production Factors
As a manufacturer, you must know that printing environments can significantly impact code quality. Humidity, temperature fluctuations, and dust can interfere with ink adherence and print clarity.
Especially in fast-paced production lines, additional issues like vibrations or inconsistent sleeve placement can further complicate the sleeve packaging code printing process.
Thus, to reduce these hazards, firms could improve their manufacturing environments. Dust filters and humidity control may assist in maintaining stable printing conditions. Furthermore, employing automation to manage sleeves throughout printing lowers the risk of human mistakes.
For example, automated methods may stabilize sleeve location on the product, ensuring consistent outcomes even during high-speed operations. It improves print accuracy while increasing overall productivity by reducing downtime and waste.
Enhancing Code Readability and Compliance
Readable codes are essential for regulatory compliance and consumer satisfaction. Smudged, distorted, or difficult-to-see codes may create significant issues like product recalls or customer dissatisfaction.
For manufacturers, this might mean financial losses and destroyed reputations. To get high-quality code, producers should focus on:
- Ink selection: Using high-contrast inks that adhere well to different sleeve materials improves readability.
- Quality Control (QC): Regular inspections during production help catch and fix any issues before the products reach the market.
- Training: Equipping staff with the knowledge to recognize and address common printing problems ensures consistent results.
Embracing Technological Advances
Nowadays, advancements in printing technology are making it easier to overcome the challenges of coding on packaging sleeves, such as sleeve detection coding technology.
This is a game-changing solution for coding on sleeves. This system uses sensors to identify specific sleeve parts and trigger printing at the perfect moment. Unlike traditional methods that rely on UV-cured inks or manual alignment, sleeve detection focuses on the sleeve itself, ensuring precise code placement every time.
This technology benefits sleeves that might shift during production, eliminating the risk of misaligned or incomplete codes.
So, automating the coding process with the right printing technology can help manufacturers reduce human error and operational costs for sleeve packaging code printing. For customized solutions, see a complete list of thermal inkjet printers here!
Looking for the perfect printing solution for sleeve packaging?
Upgrade your production with high-performance CIJ and TIJ printers that deliver exceptional clarity, durability, and compliance with industry standards.
Explore our cutting-edge coding and marking solutions today!
Referensi:
https://www.codico-distributors.com/blog/navigating-printing-hurdles-when-coding-sleeve-packaging
https://www.greenerprinter.com/blog/what-are-the-different-types-of-packaging-sleeves/
Comments (0)
Leave a reply
You must be logged in to post a comment.