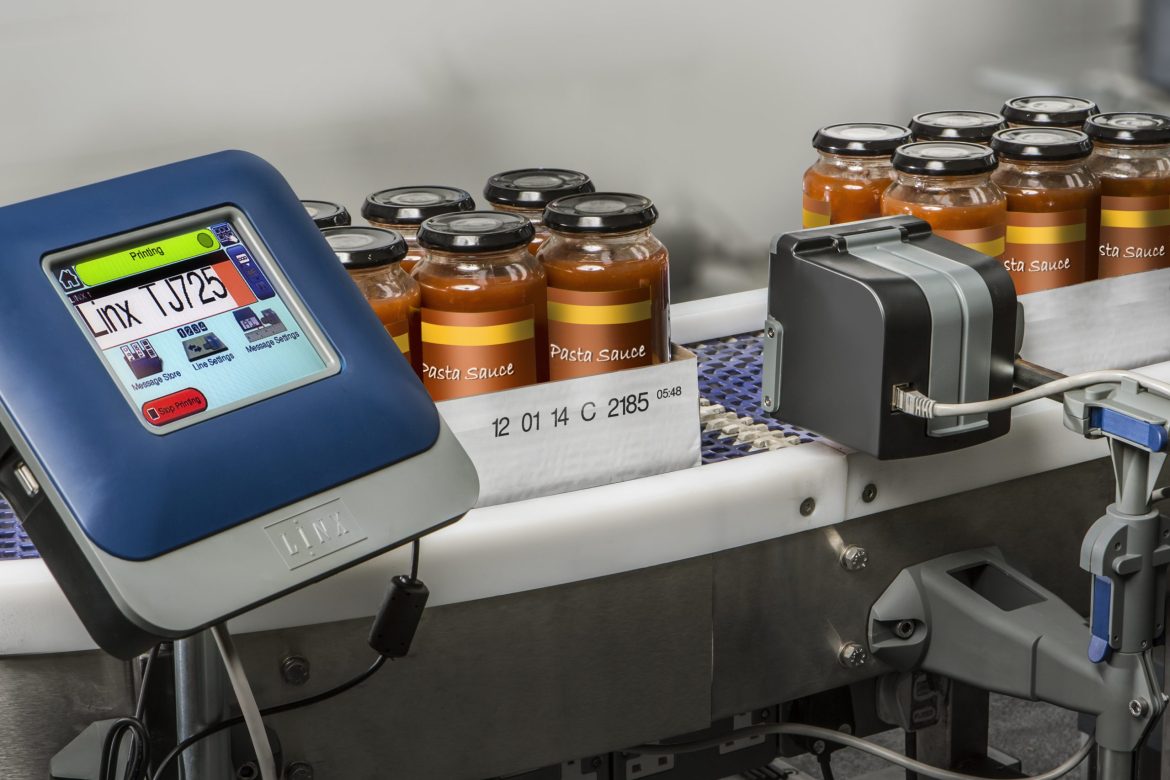
In today’s fast-paced manufacturing environment, coding and marking machines are vital for ensuring product traceability and compliance. However, operational issues can arise, leading to production delays and quality concerns. This guide provides practical solutions to common problems encountered with these machines.
However, these printers can encounter several issues that compromise productivity and cause unwanted delays. So, this article will explore some common problems faced by users of coding and marking printers and provide practical solutions for troubleshooting them.
Identifying and Resolving Print Quality Issues
First of all, why is troubleshooting the coding and marking printers important? Proper checking ensures that your coding and marking tools operate efficiently.
Frequent maintenance and timely repairs guarantee excellent prints, lower downtime, and help to avoid long-term damage. This preserves the integrity of your goods and keeps the manufacturing process free from problems.
Now, let’s discuss print quality issues regarding the coding and marking machine. These can manifest as uneven ink dispersion, hazy prints, or missing sections.
Dried ink in the printhead nozzles can sometimes cause poor print quality, mainly if a printer is idle for a long time. Therefore, achieving good print quality depends on maintaining the proper print speed and resolution settings.
Incorrect settings could result in distorted result images or even wrong print arrangement. Thus, ensure that the print speed and conveyor settings are synchronized to prevent these problems. Also, here are some examples of the common issues:
- Clogged nozzles or printheads
- Air bubbles in the ink supply
- Environmental factors, such as incorrect temperature and humidity
- Expired ink
- Maintenance routines
- Ink quality, ink smudging/bleeding, and compatibility
Read About: Best Industrial Coding and Marking Solutions for Each Industry
Dealing with Clogged Nozzles
Clogged nozzles are the first common problem in coding and marking machine on this list. Dried ink, dust, or other particles can all block nozzles, compromising the quality of printing results.
Clogged nozzles cause varying ink flow, producing partial or hazy/blurry prints. When the printer is inactive for long stretches, this can especially be troublesome since ink dries and clogs the nozzles.
Thus, regular cleaning is vital to avoid it. But don’t worry—printing equipment manufacturers sometimes already offer particular instructions on how to clean the nozzles correctly.
Maintaining a clear path for the ink also depends on cleaning solutions or wiping the nozzles with a lint-free cloth. Moreover, regular printer usage helps to lower the possibility of ink drying inside the nozzles.
Eliminating Air Bubbles in the Ink Supply
Air bubbles in the ink supply system can disrupt ink flow, producing gaps and streaks in the printed result. These bubbles can develop either during refilling or via incorrect ink cartridge handling.
Air bubbles may disturb the ink stream, thereby directly affecting the print quality of a coding and marking machine.
In this case, handling ink cartridges gently will help reduce the occurrence of air bubbles. You must also ensure that the ink levels are checked routinely and cartridges are correctly positioned.
Should air bubbles be found, certain printers have built-in features to clean the system and restore a seamless ink flow. Thus, the likelihood of air bubbles can be much lowered by following manufacturer recommendations for cartridge installation and maintenance.
Managing Environmental Factors: Temperature and Humidity
Print quality also depends heavily on environmental elements, including temperature and humidity. Extreme temperatures, for instance, might change the viscosity of the ink, making it either too thick or too thin.
Low humidity can also produce static electricity, and high humidity can lead to condensation problems. Therefore, the best performance depends on keeping the printer under control in its surroundings.
Usually, manufacturers advise running temperatures of 60°F to 95°F (16°C to 35°C) and relative humidity levels between 40% and 60%.
Temperature control devices can stabilize these conditions in the printing area. Environmental monitoring and adaptation can help your industry avoid temperature and humidity influencing print quality.
Recognizing and Replacing Expired Ink
Please note that using expired ink can lead to many print quality problems, such as fading prints, inadequate adhesion, and ink bleeding.
Remember, inks have a limited shelf life; their chemical makeup may alter once they have expired, influencing their performance.
For this problem, examining the expiration dates on all ink cartridges and using them within the advised period can help you prevent issues with expired ink.
Proper storage conditions, as specified by the manufacturer, can also extend the shelf life of ink. Replacing expired ink with fresh and new cartridges will keep the print quality consistent.
Read About: Why You Should Choose PT. DSI Printer for Coding and Marking Machines in Indonesia
Implementing Effective Maintenance Routines
Industrial coding and marking machine print quality problems can be avoided mainly through regular maintenance.
Without appropriate maintenance, problems, including blocked nozzles, mechanical failures, and software bugs, can develop, causing downtime and higher expenditures.
Conversely, well-kept printers provide better-quality prints and run more quickly. This is why establishing a routine maintenance program is especially important. This program covers firmware updates for the printer, printhead cleaning, component testing, and replacement.
Following manufacturer maintenance recommendations will help keep the printer in perfect shape. Furthermore, timely interventions and frequent inspections help prevent minor problems from becoming more serious.
Ensuring Ink Quality and Compatibility
Lastly, excellent print quality depends critically on the quality and fit of the ink with the substrate. Poor-quality ink or ink incompatible with the printing media can cause bad adhesion, smudging, and uneven prints.
Furthermore, using the incorrect type of ink can cause more frequent blockages and printhead damage. Consequently, choosing the appropriate ink for the particular use is crucial.
Manufacturers of industrial coding and marking tools sometimes offer ink type recommendations based on the substrate and printing environment. Using premium, compatible ink can help guarantee clear, crisp, and robust prints.
As an additional tip, testing several inks and substrates before full-scale manufacture can also help prevent ink bleeding and find the perfect mix for the best print quality.
Knowing and troubleshooting these common print quality problems can help ensure your coding and marking machine runs smoothly and produces high-quality prints. For the best tools, see a complete list of continuous inkjet printers here.
Experiencing issues with your coding and marking machines? Contact DSI today for expert support and solutions tailored to your industrial needs.
References
https://www.kaocollins.com/inktank/troubleshooting-thermal-inkjet-coding-problems/