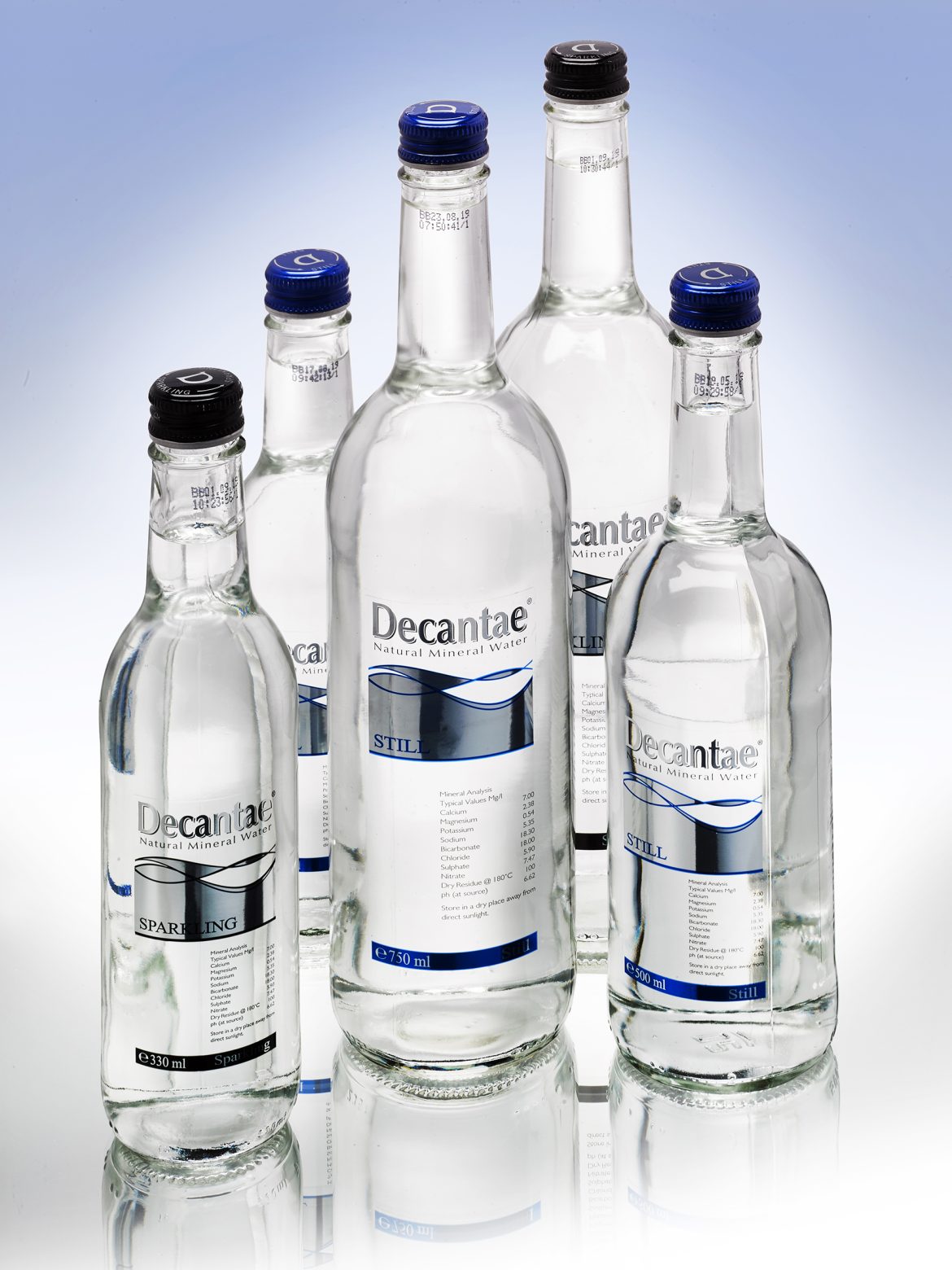
Precise and robust labeling is vital in beverage coding and marking. Whether your products are kept hot, humid, or cold, you want to ensure that your labels stay readable and adhere to.
Distinct surroundings may create distinct labeling issues, so recognizing these can help you choose the suitable materials and techniques to keep the integrity of your labels and brand image. Let’s read the guide here.
Choosing the Right Labels and Adhesives
Selecting the appropriate labels and adhesives will help you to ensure that your labels perform under several environmental conditions.
This means labels must withstand the specific humidity levels and temperatures they encounter throughout storage and transit. Here are the tips:
Temperature Sensitivity
In beverage coding and marking, temperature sensitivity affects the label. Labels could bend, peel, or fall off in hot or humid environments.
Overly soft adhesives can make labels challenging to remove from the roll or cause them to stick to the roll instead of the product. These problems might jeopardize the labels themselves or distort the labeling process.
Proper label roll storage is crucial for dealing with these issues. This encompasses keeping the rolls straight to eliminate sliding, storing them in plastic bags to reduce humidity exposure, and maintaining them at lower temperatures to avoid heat contact.
Moreover, good storage can significantly enhance label performance in high-temperature settings. These are some best practices for properly keeping label rolls in extreme heat:
- Have label rolls sit straight forward. If at all possible, do not lay them flat to stop slipping on the liner.
- Store them in plastic bags to prevent humidity exposure.
- Store them lower to the ground to minimize their exposure to top-shelf temperatures that can be 20° to 30° hotter.
- Fan the label stack to enhance label handling.
- Store them on a multipurpose rack fitted for hanging dowels.
- Stack them end to end.
Cold Storage and Freezing Conditions
For beverage coding and marking of products kept in cold or freezing temperatures, special label materials with selected adhesives are needed. The label must withstand extreme cold, wetness, and varying application conditions across the cold chain.
So, labels for cold environments must satisfy several standards, including sticking despite temperature gradients and remaining intact under moisture and condensation.
Besides food and drink, labels for cold applications are also commonly used in industries such as cosmetics and medications. These labels must be strong and maintain their adhesive properties in the most demanding surroundings.
Read About: Industrial Coding and Marking Systems: Where to Start?
Application Techniques
Robust and precise labeling of your beverage products will help to define compliance and brand image. To achieve this, specific beverage coding and marking techniques are necessary, such as:
Proper Surface Preparation
The surface on the code or label laid upon needs to be dry and clean. The surface on which the code or label will be laid needs to be dry and clean. Dirt, dust, or moisture could cause the adhesive to stick incorrectly, causing invisible codes or labels to peel off.
For example, cold-environment bottles could have condensation, which must be eliminated before applying labeling or codes.
In this case, using clean surfaces promotes excellent adhesive adhesion, thereby preventing issues during storage and transportation.
Correct Application Pressure
Applying the correct pressure is just as important as preparing the surface. While too little pressure could cause labels not to cling correctly, too much pressure could ruin the label or the container.
As such, providing even enough pressure throughout the entire label or code area is necessary.
By frequently checking and fixing the tools for applying labels and codes, you may ensure correct pressure and guarantee high-quality labeling every time.
Material Selection
In beverage coding and marking, selecting of proper materials should also be considered, as it can affect the label’s durability in any temperature or season. Here’s the guide:
Polypropylene and Polyethylene Labels
When it comes to beverage labeling, choosing a suitable material is essential for both aesthetics and functionality. Two popular options are polypropylene and polyethylene labels.
Polypropylene labels are well known for their high-temperature resistance and durability. They are excellent materials for outdoor gear, chemical items, automobile parts, and those subjected to demanding handling or severe conditions.
They are also strong and long-lasting, ensuring the label remains legible and transparent throughout the product’s lifetime.
Conversely, polyethylene labels are more flexible and water—and chemical-resistant, so they are less costly for products that do not require high-temperature resistance.
These labels are widely used in food packaging and cosmetic products where few hostile environments are involved.
Additionally, polyethylene labels are soft and flexible and easy to glue to many surfaces; however, they might hold up better under extreme heat or treatment than polypropylene labels.
Waterproof Inks and Coatings
From refrigeration to ice buckets to customer use, labels in the beverage industry must typically withstand moisture. Guaranturing labels remain clear and readable depending entirely on waterproof inks and coatings.
Waterproof inks for beverage coding and marking ensure that vital information, including branding, nutritional data, and barcodes, is legible. They are designed to withstand blurring and fading in water.
As for waterproof labels, you may use coatings. Coatings include varnishes and laminates provide still another level of protection. Laminates are film layers applied over the printed label, making them waterproof and scratch-resistant.
You can also use varnishes or liquid coatings that cure or dry on the label surface, so offering durability and moisture control. While all laminates are waterproof, ensuring the adhesive used with the labels is water-resistant is essential.
Read About: Coding and Marking: Ways to Optimize Efficiencies in Every Kinds of Product
Environmental Considerations
Sustainability is a growing priority in the beverage industry, because according to a study, most consumers nowadays are eager to pay more for environmentally friendly packaging.
A recent survey by NielsenIQ found that 73% of global consumers are willing to change their consumption habits to reduce environmental impact, while 41% are ready to pay a premium for sustainable products. This highlights the importance of integrating eco-friendly solutions in beverage labeling and packaging
One significant aspect is the choice of beverage coding and marking materials. Selecting ecologically suitable label materials, such as those developed by engineers, can significantly reduce the environment’s impact.
These materials, including wash-off film labels, enable them to reach recyclability goals without compromising the label’s usefulness or appearance.
This approach appeals to consumers who are gradually ready to pay extra for ecologically friendly packaging in addition to helping to protect the surroundings.
Furthermore, beverage companies should give considerable thought to the complete lifetime of their labels. This relates primarily to glass and PET containers and how labels interact with recycling methods.
For PET containers, for example, wash-off treatments allow the label to float off during washing, enhancing recycling efficiency.
Regular Maintenance and Monitoring
Ensuring constant efficiency and quality depends entirely on maintaining and testing coding and marking tools. Regular inspections help prevent common problems, such as label dispensing mistakes caused by temperature variations.
For instance, high temperatures might weaken adhesives, allowing labels to stick to the roll rather than the goods, causing operational delays and applicator jams.
One beverage company implemented temperature-resistant adhesives in its labeling process, reducing downtime due to applicator jams by 30% and improving overall production efficiency. This example demonstrates the value of investing in high-quality materials tailored to specific environmental conditions.
Correct storage of label rolls may reduce specific issues.
Moreover, a comprehensive monitoring system would support a more reliable and accurate labeling procedure.
Advanced monitoring tools, such as IoT-enabled sensors, can provide real-time data on temperature and humidity during the labeling process. These tools not only reduce operational inefficiencies but also enhance product traceability, ensuring compliance with industry standards.
For example, sensors or data loggers can alert operators to deviations from the designated range, therefore maintaining the quality and safety of the labeled products.
Beside integrating these beverage coding and marking best practices, consider using continuous inkjet printers. These printers offer flexibility and efficiency in applying high-quality labels under any conditions. See a complete list of continuous inkjet printer here.
Ready to optimize your beverage labeling process? Explore our range of continuous inkjet printers designed for precise, reliable, and eco-friendly coding solutions. Contact us today for a consultation and discover how we can enhance your production efficiency!
References
https://www.diagraph.com/blog/how-do-i-get-labels-to-stick-in-hot-and-humid-environments
https://www.linkedin.com/advice/3/what-best-way-avoid-temperature-abuse-food-products-jzktf
https://www.weber-marking.com/blog/hot-tips-for-cold-temperature-labeling/
https://www.upmraflatac.com/labels-by-industry/beverage-labels/
https://www.pro-motion.ws/blog/waterproof-labels-for-plastic-bottles/
Comments (0)
Leave a reply
You must be logged in to post a comment.