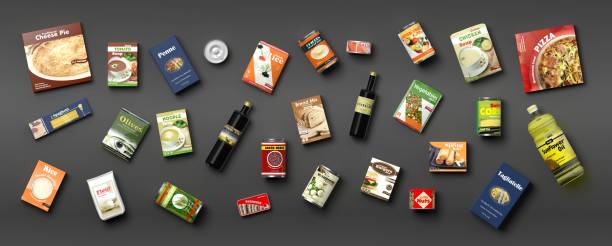
Ensuring that product labels in today’s highly regulated food sector are clear, readable, and compatible with many laws is absolutely vital. Food product labels serve not only for aesthetic appeal but also for following criteria established by authorities.
This implies that every element on a label, including lot codes and expiration dates, has to be precisely legible to prevent possible fines and product recalls. Understanding print resolution and code readability is one of the main elements that ensures this.
Importance of Print Resolution
The clarity and quality of printed codes and text on food packaging depend critically on the print resolution, measured in dots per inch (DPI). Higher DPI, or the number of dots a printer can generate per inch, results in sharper and more detailed images.
So, selecting the correct DPI can make a significant impact on the packaging of food products, where accuracy is essential. Here is some helpful advice:
High vs. Low DPI
There are various commonly used DPI ranges on printers, including 203/200, 300, 406/400, and 600 DPI.
High-DPI printing tools, such as 600 DPI, provide much sharper and clearer images compared to lower ones, such as 203 DPI.
This is particularly important for printing barcodes, QR codes, and small text, where even minor imperfections can lead to scanning problems or misinterpretation.
A 600 DPI printer, for example, can produce quite clear barcodes and small text that scanners would find readily readable. On the other hand, a 203 DPI printer could struggle with finer details yet be enough for more extensive text and simple barcodes.
Choosing the Right DPI for Your Needs
Overall, selecting the appropriate DPI for food products depends on your needs. A 203 DPI printer is sufficient for large labels or shipping tags with large text and barcodes.
However, to preserve readability and prevent problems, a 300 or 600 DPI printer is advised for more detailed labels, such as those with small fonts or complex designs.
Read About: Variants Continuous Inkjet Printer To Batch Coding For Multiline Packaging
Key Considerations for Code Readability
To ensure that your food products codes and text are easily readable, several factors need to be considered beyond just DPI, such as:
Printing Materials
The choice of printing medium guarantees simple code reading. Your chosen materials must be strong enough to resist environmental factors and handling without compromising print quality.
For example, a reflecting or glossy surface could make the scanning process challenging, so selecting a material that fits your requirements and ensures good readability is crucial.
Printing Techniques
The final quality of your labels can vary depending on the printing method you use, such as offset, digital, screen printing, or another. Your budget, volume needs, and desired print quality should all guide your decision on technique.
Ink and Toner Quality
Printing sharp and clear prints requires using high-quality ink or toner. Bad-quality ink could cause blurring or smudging, affecting readability. So, to keep high standards, make sure your printer runs premium ink.
Surface Smoothness and Size
The readability of your print area depends partly on its surface texture and size. While a QR code too thin could be challenging to scan, a rough or uneven surface might distort printed codes. So, aim for a balance between size and clarity.
Best Practices for Enhancing Code Readability
How can we improve the readability of food products’ codes in packaging? Here are some best practices for you to follow:
Use High-Resolution Images
Always use high-resolution images for your codes. Blurred or pixelated codes could cause a bad user experience and scanning problems. Make sure your pictures are sharp and straightforward to make simple scanning possible.
Optimal Placement
Next, put place codes at an easily seen location at eye level. Steer clear of confusing many codes cluttering the space. Including a call to action (CTA) such as “Scan Me” can also help to ensure people know what to do and boost actions to check the code.
Test Your Codes
Always test your codes on several devices and under several conditions before mass production. This guarantees that the codes operate as expected in practical settings and helps find any possible problems.
Regulatory Compliance
Several rules must be followed when packaging food products to guarantee openness and safety. These regulations often include requirements for lot codes, expiration dates, and barcodes.
For example, the regulation of the Fair container and Labeling Act (FPLA) in the US requires that container labels accurately state the contents and expiration of the products.
Also, depending on the types of products, food manufacturers often must label the packaging with the following types:
- Expiration dates
- Batch/lot codes
- Serial numbers
- Barcodes or data matrices
Following necessary rules not only helps prevent legal problems but also increases customer confidence. Therefore, make sure your labels reflect any changes in regulatory requirements and satisfy all required criteria by constantly updating them.
Overall, well-written and readable codes improve user experience and help to prevent expensive mistakes and recalls. For top-quality machines that can handle all your food products printing needs, see a complete list of thermal inkjet printers here.
References
https://inkjetinc.com/blogs/default-blog/industries-food-packaging-marking-coding-ij
https://www.uniqode.com/blog/qr-code-best-practices/qr-code-printing-guideline
https://www.peaktech.com/blog/barcode-printer-dpi-what-you-need-to-know/
https://www.accuratelabels.co.nz/what-thermal-printer-dpi/
Comments (0)
Leave a reply
You must be logged in to post a comment.