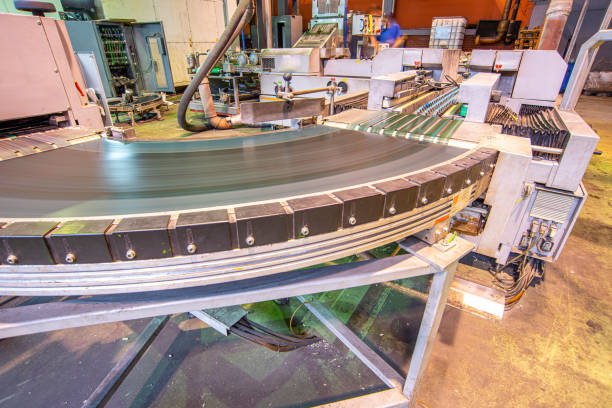
Printing on uneven or irregular surfaces requires specialized methods and meticulous considerations. Maintaining the print quality and consistent ink deposition are often the primary challenges.
Industries such as FMCG, pharmaceuticals, and automotive frequently print on curved materials like bottles, pipes, and cans. Without the right technique, prints may smudge, misalign, or fade quickly, leading to wasted materials and production delays. Choosing the right printing technology ensures high-quality and durable markings, even on complex surfaces.
With the right technology and advanced methods, these challenges can be effectively addressed. Let’s explore the key aspects of addressing these challenges below.
Challenges of Printing on Curved and Irregular Surfaces
Clean and well-defined print across the entire surface can be challenging to achieve when printing on curved surfaces or contours. Several factors must be carefully considered, increasing the complexity of curved surface printing. Below are some of the challenges that are commonly faced in the sector.
How to Prevent Uneven Ink Distribution and Misalignment
Due to irregular surfaces, there may be differences in ink thickness, resulting in some parts being lighter or even darker than the others. Additionally, it can cause misalignment issues, making it difficult to precisely align the print design.
Solving Ink Pooling Issues for a Cleaner Print
Ink pooling occurs when wet ink spreads unevenly or mixes with excess ink. This can be an issue because the low points on the surface can trap excess ink, producing sloppy, and uneven prints.
To prevent ink pooling, printers can adjust drying time, use fast-drying inks like UV-curable inks, or modify the angle of ink application for better control over deposition. Additionally, controlling ink viscosity ensures a more consistent application, preventing excessive spreading on non-flat surfaces.
Material Compatibility and Printing Accessibility Challenges
The degree of ink adhesion varies across materials, requiring specific inks and printing methods to ensure lasting print quality.
For instance, glass and plastic require high-adhesion inks, while metals may need a primer to enhance ink bonding. Choosing the right pre-treatment method, such as corona treatment for plastics or plasma treatment for metals, ensures the ink adheres well and remains durable over time.
On the other hand, a complex shape of printing materials may cause the printing head to be difficult to reach, which would limit accessibility.
Choosing the Right Printing Technology
Selecting the right printing technology is necessary for the irregular surface printing industry, like plasterboard manufacturing. The curvature, shape, material, and size of the object along with the durability and quality of the ink are all important considerations.
However, specific requirements may lead to different concerns and priorities. Here are a few suggestions to help you make the right choice.
Pad Printing
Pad printing is specifically designed to transfer images on curved surfaces. It works by utilizing a flexible silicone pad that follows the shape of the object. In particular, it can deliver high-quality prints on complicated shapes, making it ideal for products like bottles, pens, and golf balls.
Screen Printing
With careful technique, screen printing can be applied to slightly irregular surfaces, such as bottles and plastic pieces. However, it is not the best option for detailed graphics on complex shapes.
Inkjet Printing
With the help of adjustable print heads, inks, and nozzles, inkjet printing can be an ideal choice for printing uneven surfaces. Continuous inkjet (CIJ), thermal inkjet (TIJ), and handheld inkjet printers are among the top choices for this industrial application. They can print on materials like cardboard, plastic, metal cans, and glass bottles.
Inkjet printing is particularly effective for printing variable data such as batch numbers, expiration dates, and barcodes. Unlike pad or screen printing, inkjet technology eliminates the need for costly plates and screens, making it ideal for high-speed production lines requiring flexibility.
Read About: Overcoming Coding Challenges in Plasterboard Manufacturing
Optimizing Ink and Adhesion for Better Results
To obtain optimal results for irregular surfaces printing, you need to optimize the ink and adhesion. Using specialized inks for uneven surfaces is highly recommended. Here are three kinds of ink to use on uneven surfaces.
Flexible Inks
This type of ink is designed for flexible materials. It can conform to the contours of curved surfaces without cracking.
High-adhesion Inks
High-adhesion inks are exquisite for printing on materials that need strong bonds such as glass bottles. It sticks well to a substrate and can prevent ink from flaking or rubbing off.
UV-curable Inks
UV-curable inks are the best option if you want inks that dry more quickly on irregular surfaces. It can enhance adhesions on a variety of materials, which significantly improves the printing quality and its success rate.
Advanced Techniques to Mitigate Printing Artifacts
Printing artifacts are unintended imperfections that affect the appearance and usability of printed products. However, you can minimize printing artifacts by adjusting the settings of the printer, such as the print speed, layer height, and temperature.
On top of that, you also need to calibrate the print bed, cleaning the printer nozzles, tightening belts and screws to stabilize the printer, and ensure you are using good quality filament.
Incorporating Automation for Consistency
Automation in printing technology offers significant benefits, such as increasing productivity, reducing errors, and enhancing print quality. As a result, it will assist businesses in scaling up operations and meeting customers’ expectations.
A continuous inkjet (CIJ) printer is considered a highly automated printing technology. It automatically generates ink droplets and produces prints without manual intervention.
Additionally, automation in printing reduces human error and ensures consistency in every batch. Smart printers with IoT connectivity can track ink levels, monitor print quality, and send alerts for maintenance, minimizing downtime and improving production efficiency.
So, by using this technology, you do not need to update variables manually.
Its non-contact printing method enables seamless printing on curved, uneven, and irregular surfaces. This makes it ideal for marking items such as bottles, pipes, and more. For further recommendations, see a complete list of continuous inkjet printers here.
Looking for the best printing solution for curved surfaces? Discover our latest continuous inkjet printers designed for precision, speed, and reliability. Browse our full range of industrial inkjet printers now!
References
https://www.inkcups.com/inkjet-printing-on-curved-surfaces/
https://www.theleeco.com/insights/increasing-print-quality-in-industrial-inkjet-systems/
https://www.linkedin.com/advice/0/how-can-you-print-graphics-irregular-surfaces-like-bottles-syojf
Comments (0)
Leave a reply
You must be logged in to post a comment.